The first numerically controlled machine tool appeared in 1952 (MIT). It was developed in the United States, starting in 1942, to meet the needs of the aviation industry – making various shapes in large aluminum helicopter propeller blades, all of which are complex surfaces.
The evolution of this product has increased the capabilities offered by this type of order, favored integration into the construction of automated equipment and ensured real-time data processing.
Machines with modern numerical control
The use of numerical control (CN) is not limited to machine tools, it is also present in laser beam cutting installations, electro-erosion treatment, assembly operations and others.
Today, parts production cannot be considered feasible without numerically controlled machine tools. With this tool, any shape can be produced with an accuracy of more than 90%.
When machining complex surfaces with conventional ones, before performing the actual machining process, it was necessary to make a wooden prototype, which was then scanned and copied with variable precision to a new part. This process was considered too much of a waste of materials and human resources. So many employees have worked for many days on a complex piece that, at present, can be produced in a very short time and with very high accuracy.
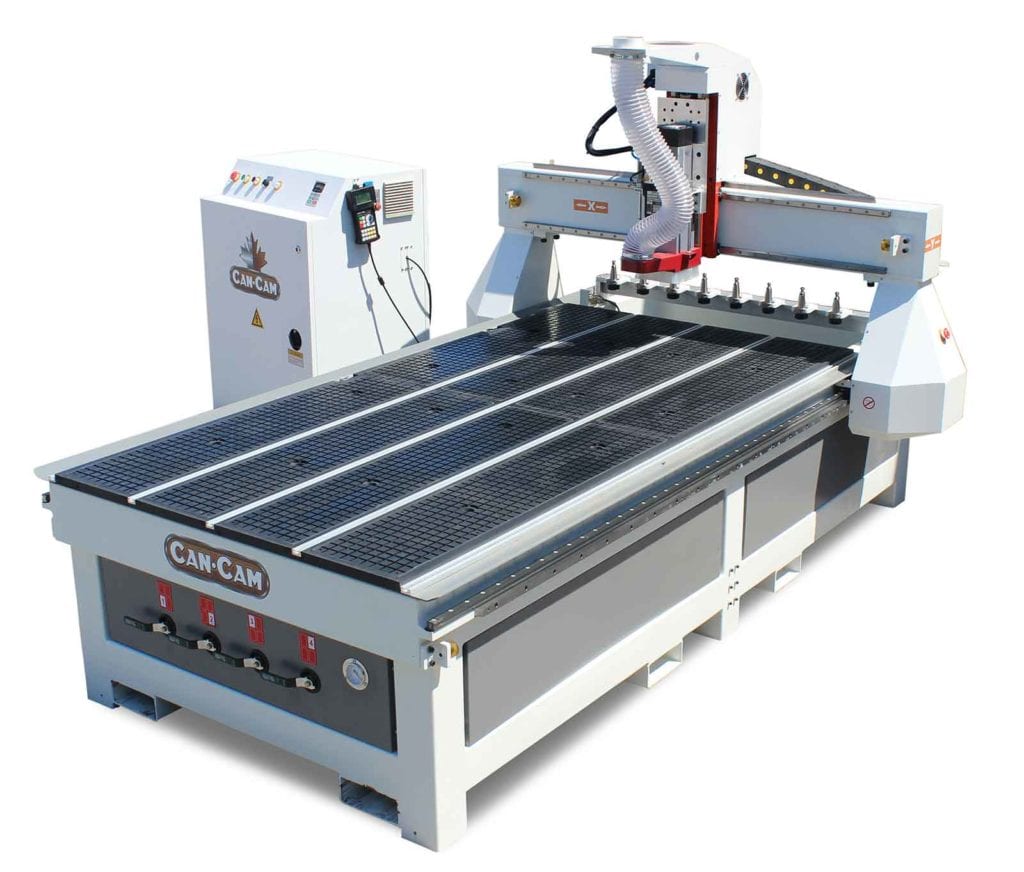
What is a CNC Router?
The numerical control machine tool consists of two components: the machine itself and the numerical control equipment. It executes ready movements with respect to each specific axis, which the program considers.
The numerical command introduced the notion of axes as linear displacement or rotation. These movements are performed by the moving bodies – or parts – of the car. Generally, such a model has 3 translation axes and 3 rotation axes. To these 6 can be added others, which actually depend on the device. Because of their complexity, they need to be of the highest quality, like the ones you can find at elephant-cnc.com.
If you are a beginner, we have some ideas for you:
Laser engravers
Depending on the type of material and its thickness, both the strength and speed that are adjustable for engraving and cutting vary. Thicker and harder materials are always cut at low speeds, and usually at maximum power.
The size, appearance of the laser desktop, as well as the technical parameters vary depending on the need and its most common purpose. Thus, there is a smaller model of laser designed primarily for stamping, a laser whose work table in the form of metal rungs is intended primarily for cutting, a model with a desk in the form of a honeycomb designed primarily for the purpose of engraving, but also for cutting, etc.
With laser technology it is possible to satisfy many needs of engraving workshops, production of stamps, nameplates, nameplates, ID badges, production of unique advertising materials, unique gifts, pendants, etc.
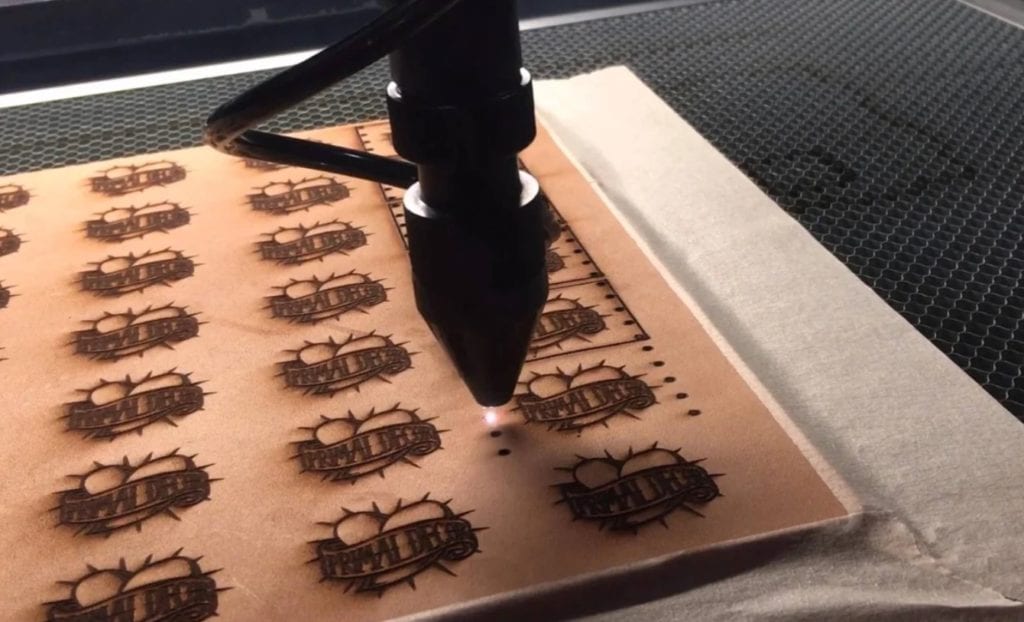
Milling machines
They are designed for seamless machining of metals, plastics and other materials. The secret to quality milling is surface quality and short cycle times.
To achieve these results, manufacturers need a fast main opening, intelligent software and a versatile CNC system that can harness the full potential of machines depending on different materials and production needs. But to be sure you have a positive impact, you need another element – solid reliability.
Depending on the material being machined, dilation during the milling process can affect the radius and/or length of the instrument and the main shaft. Intelligent thermal control and compensation functions on advanced machines ensure this and repeat accuracy regardless of the process.
Lathes
These are scrapers and are practically irreplaceable. It is one of the oldest working tools and is used in many fields, from mechanical engineering to carpentry. Usually, lathes consist of several parts, namely: bed, storage box, gear, frame, liners, and support sled. Further lathes are divided into several types, used for different purposes.
Among the parameters that make it easier to choose the best and most suitable lathes are: constant or variable speed, and the aforementioned digital capability (drilling depth display), a tightening spindle to perform the safest work, the distance between the tips, all dimensions, diameter and width of the scraper, of course, and sheer strength, durability and metric threads.
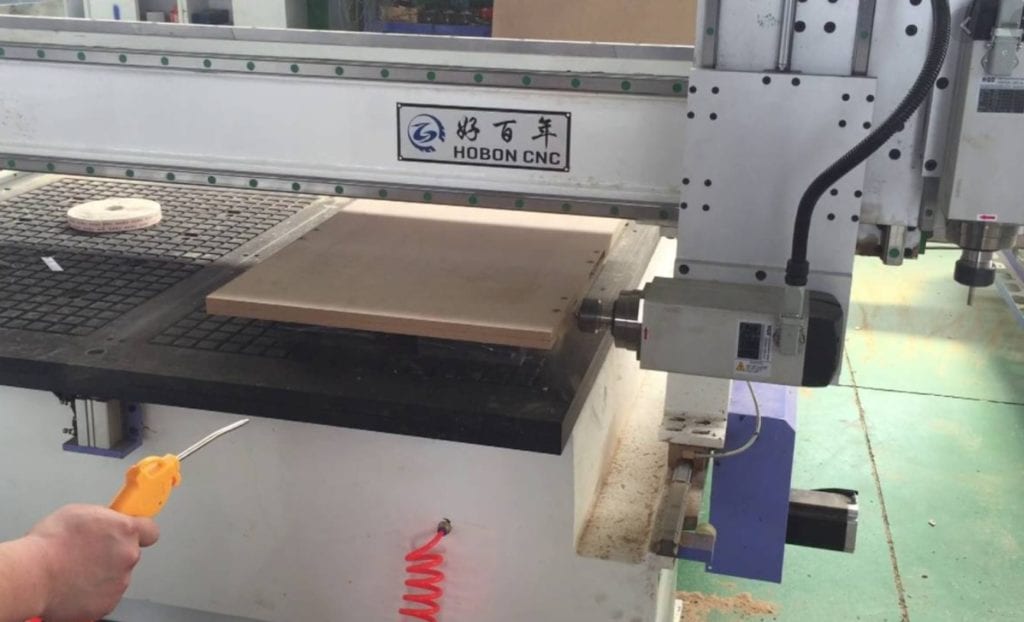
Drilling machine
It is a very advanced type of CNC router. You can program the move as well as drill holes. It does the job very effectively. It is mostly used for drilling panels for sound isolation.
Wire bending machine
Automation enables complete control of the production process through technological simulation, monitoring and statistical analysis of production, automatic sorting of manufactured parts and finished products.
This is a technical and technological solution for automatic production such as: shelf production lines for dishwashers, shelf lines, counters and other retail equipment, production lines for fans and air conditioning grilles and similar integrated production systems.
Unlike dedicated wire bending machines – the CNC concept allows flexible manufacturing that allows small batches, prototype / unique product and opens the possibility of service. Computer feedback control guarantees uniform characteristics of the bent parts, and the user environment for visual programming and simulation reduces the preparation time, that is, reduces the total fixed costs that precede the production of the first piece.
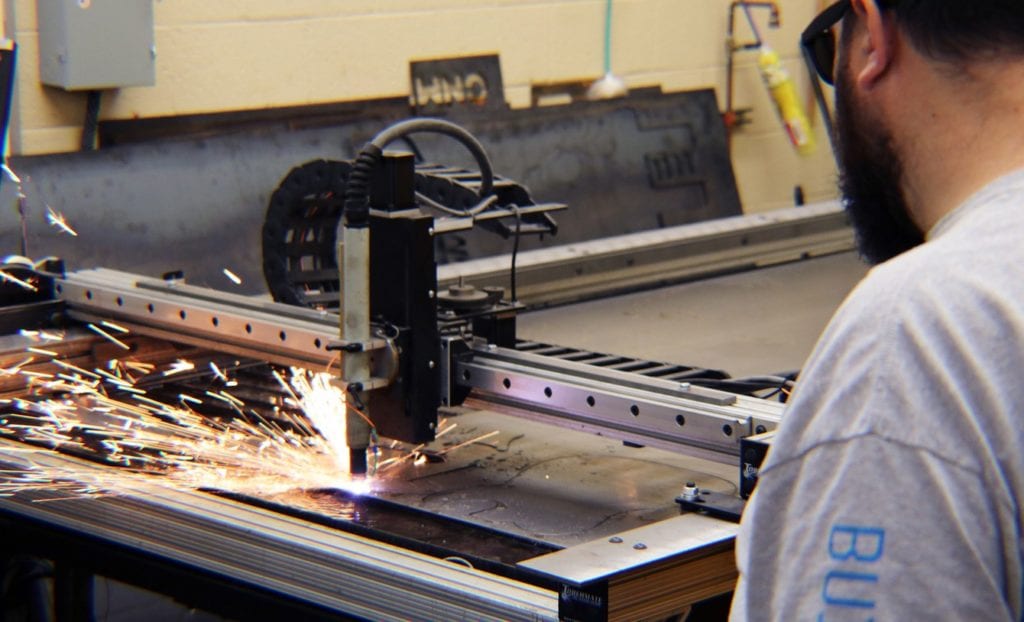
CNC plasma cutting
Sheet metal is a thin sheet of metal or metal alloy. Once upon a time, sheet metal was made solely and exclusively from iron, but later other metals, alloys, and various non-metallic additives were introduced into production. It is also interesting that in the beginning, the sheet metal was manufactured only by the masters of sheet metal, but today it is part of the work of various workshops and factories, which in addition to the production of sheet metal, offer its processing, such as bending, cutting and the like. Visit Weldaloy and check some of their products made from titanium and other materials.
Modern technology and its enormous development have brought novelties to everything, and so sheet metal cutting has become more modern, precise, faster, easier, simpler … CNC cutting – metal cutting, or sheet metal cutting. So this is a process where the heat source is actually an electric arc. It has been in industrial use since 1960, so it is used for cutting various types of metals that are electrically conductive.
The CNC plasma metal cutting process mainly cuts materials that are up to one hundred millimeters thick, but can also be used to cut very thin materials – for example, up to one millimeter is common. You may also be interested in the answer to the question of how quickly a CNC machine cuts, ie. during which time he completes the work. The answer is that cutting speeds are extremely high, and therefore this plasma metal cutting process is considered to be very productive and efficient.
Conclusion:
If you have opted for numerical control, it is certain that you will have more success using small batches and producing unique pieces, even if they have heavy shapes or patterns. You just have to choose the right model. Make a smart decision and elevate your production development to a higher level by enabling you to improve quality, reliability and flexibility.