Plastic plays a huge role in many different manufacturing-based industries, and although it’s not the most community-loved material that we have, it surely is one of the most practical ones. There are many different ways to manipulate with plastic and get the desired results, but one of them stands out, and today we’re going to tell you more about it.
This method is called Injection Molding and it’s a very widely-used one, so we feel like more people need to know what exactly is happening throughout the entire procedure. If you happen to be interested in getting a job that involves the use of injection molding, or you’re just curious to learn some more on this subject, make sure to stay with us until the very end of this article. Let’s take a look at the five basic steps of the IMP.
1. Choosing the right materials
The quality of the final product is impacted by two very important things. The first one is how carefully the entire process was carried out, including the shape of the mold and the temperature on which the materials were heated to bend properly. The second one is the actual quality of the materials and the plastic, which is something that cannot be neglected if you want a final product that meets the industry standards.
Choosing the right materials is the first step and the one that will have the most impact, so make sure that you’re supplying from a reliable source. One of the main perks of living in an internet era is the fact that you can find so many manufacturers to help you with your designs, even if you’re completely inexperienced in this field. Stebro-mold for example is a website where you can order such service, starting from the very basic part-design up to the final delivery of your product.
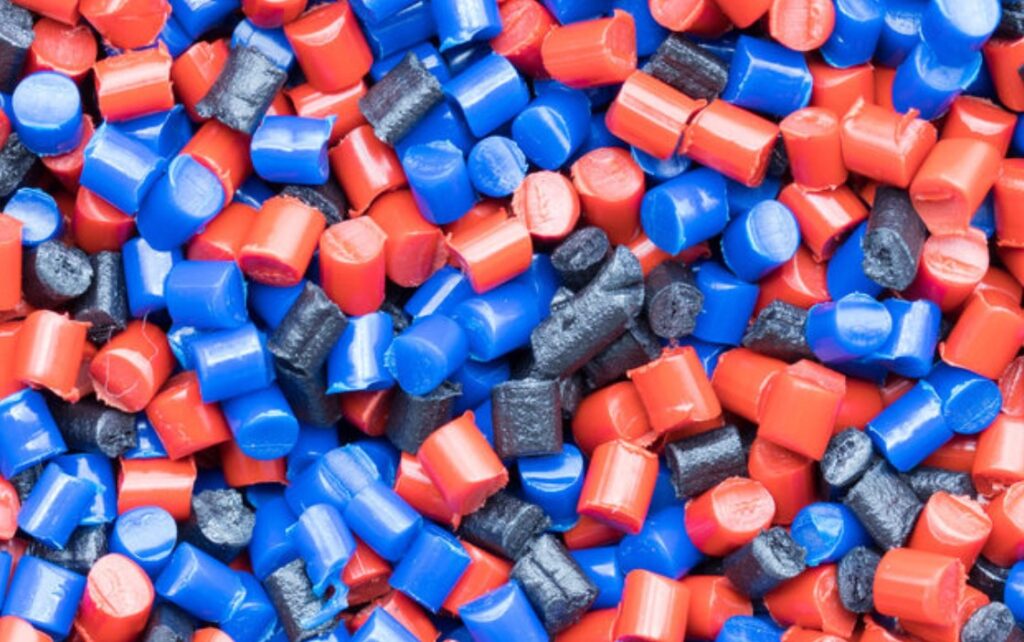
2. Heating the plastic
You cannot fit a plastic cube into a mold that has the shape of a cylinder, and it won’t work if you reverse all this as well. This is why it’s very important to heat the materials to a degree where they can fit anywhere due to their liquid form. Now there are numerous ways of doing this, and many factories have their methods, but in reality, it doesn’t matter how you’ll do it, it just matters that you get the plastic up to the required heating degree so that it becomes liquid. After you’re done with this, it’s time to inject the heated and liquidized material into a mold, but first, you need to choose the right one to inject into.
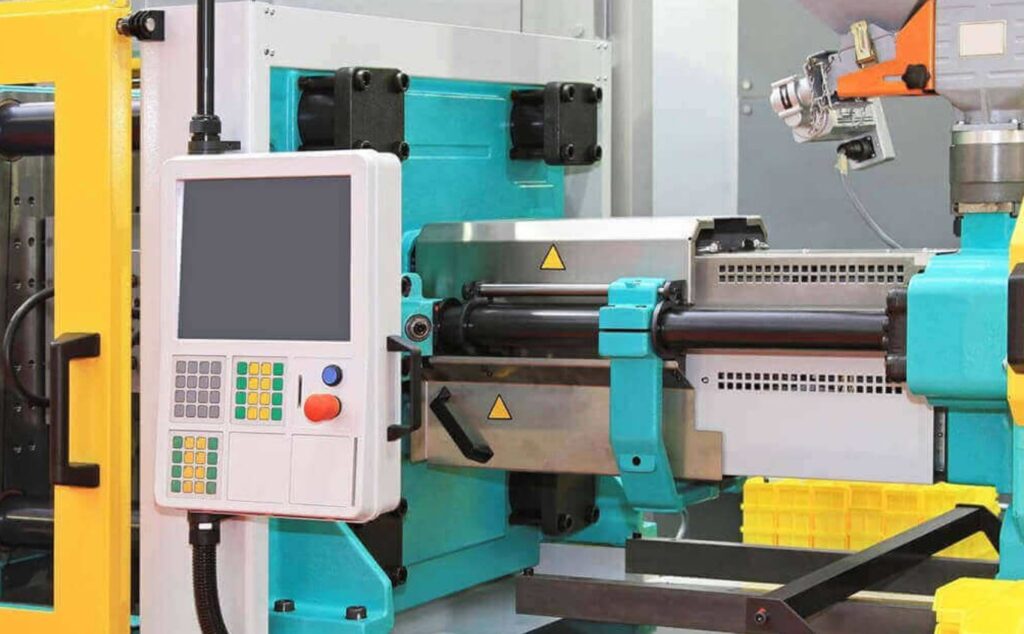
3. Creating or choosing the right molds
Depending on the previously-made designs, and your idea of how the final product should look like, you need to choose the right form of mold. Although it sounds like something very simple to do, factories who use this technique usually produce items in large quantities, so they cannot just change one mold unless it’s for a prototype. If they want to change the design of a certain product, they’ll need to change so many molds and that’s quite the investment. On top of this, a total recalibration of all the machines and robots is also needed in case the entire mold frame is changed. Sometimes smaller businesses create their molds which they use for their specific designs.
After you’re done with all this, it’s time to inject the heated plastic into the mold, and here’s how that’s done.
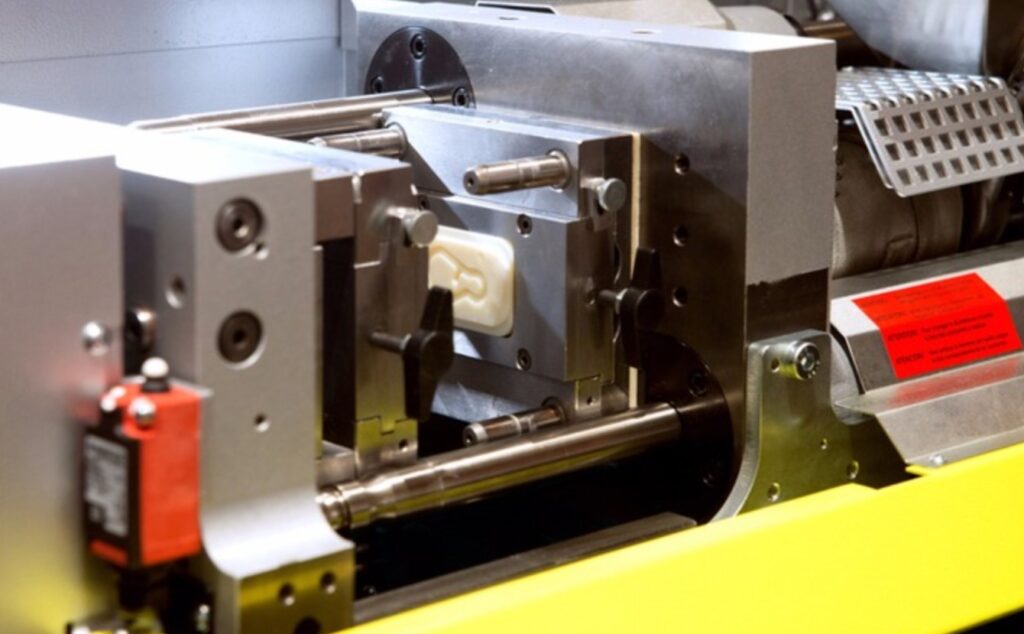
4. Injecting the plastic and cooling down
The so-called “molds” are not as simple as some would think. They are connected with a few automated parts that make sure everything is going right during the procedure. For example, when the liquidated plastic starts being injected into one of the molds, the air starts to escape through vents into something that’s called an injection pin. The gate and the vent all together have the role of making sure that the mold is properly and filled before continuing. Once everything is filled up properly, the waiting game begins.
The cooling time will mostly depend on the type of plastic that’s used in the process, but some molds have internal cooling systems such as the “heatsinks” for example, through which the heat can escape when the plastic is cooling down. After the cooling step is done, the mold opens and the so-called “ejector” pushes the part down, where it falls on a trail and moves towards the quality-control and inspection area.
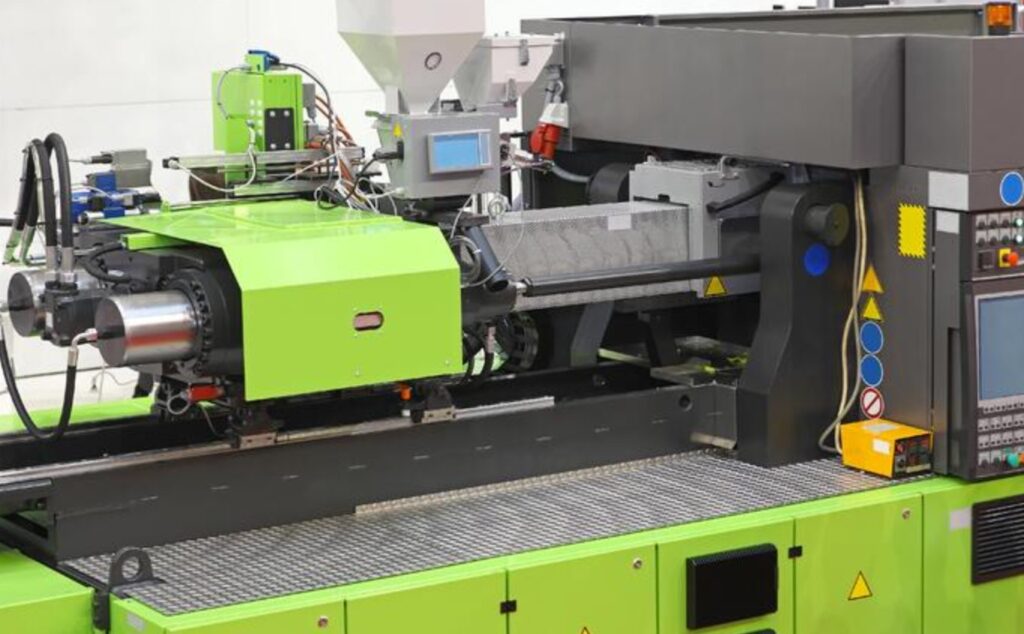
5. Inspection and quality control
When everything is cooled down properly, a process of inspection and quality control begins. In some factories, this is done by real humans who have the task to make sure every part is identical and without any errors. However, in some factories, usually, the ones that produce thousands of parts per day, quality control is done by a robot. Whether this method is superior compared to the one where humans are doing the inspection is still not decided, but that’s just how things with technology are these days.
Depending on the type of parts that are being produced, the ones with an error are usually sent into a place where the plastic gets re-melted and the entire procedure begins from zero once again. This doesn’t happen in every industry though, but more and more factory-owners are aiming to use recycling as a way to save resources and reduce pollution.
https://www.youtube.com/watch?v=cggVJL_9yZM
Conclusion
Many of the plastic products that we have at home nowadays are made using the injection molding process. This is a very useful procedure for creating almost any type of plastic items, but especially useful for scenarios where the final product needs to be in a shape that’s considered to be a bit more complicated. According to a few public statistics, about half of all plastic items that we have on the market these days are made using the injection molding technique. In today’s article, we listed the five most basic steps of the process.